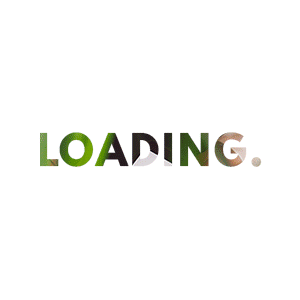
Process_Optimisation
Be more efficient and effective
We help you identify, prioritise and deliver opportunities to improve your business processes. Using lean six sigma techniques, we enable your team to identify current challenges and appropriate solutions, including the potential for digital tools. We combine this thinking with our own objective observations, to create a priotised plan of action - which is then delivered.
Approach
Our approach is based around 4 stages: Client Engagement, Business Discovery, Improvement Delivery and Continuous Improvement
- Client Engagement: We gain an understanding of your objectives, the business context and current pressures
- Business Discovery : We use the development of an Enterprise Process Map, or a Process audit to build an optimisation plan
- Improvement Delivery: We carry out value stream, kaizen, process mapping and digital workshops, and train the team to deliver their own kaizen sessions
- Continuous Improvement: We provide coaching and training support for the team on an ongoing basis to sustain focus on the priorities
Process Optimisation Workshop
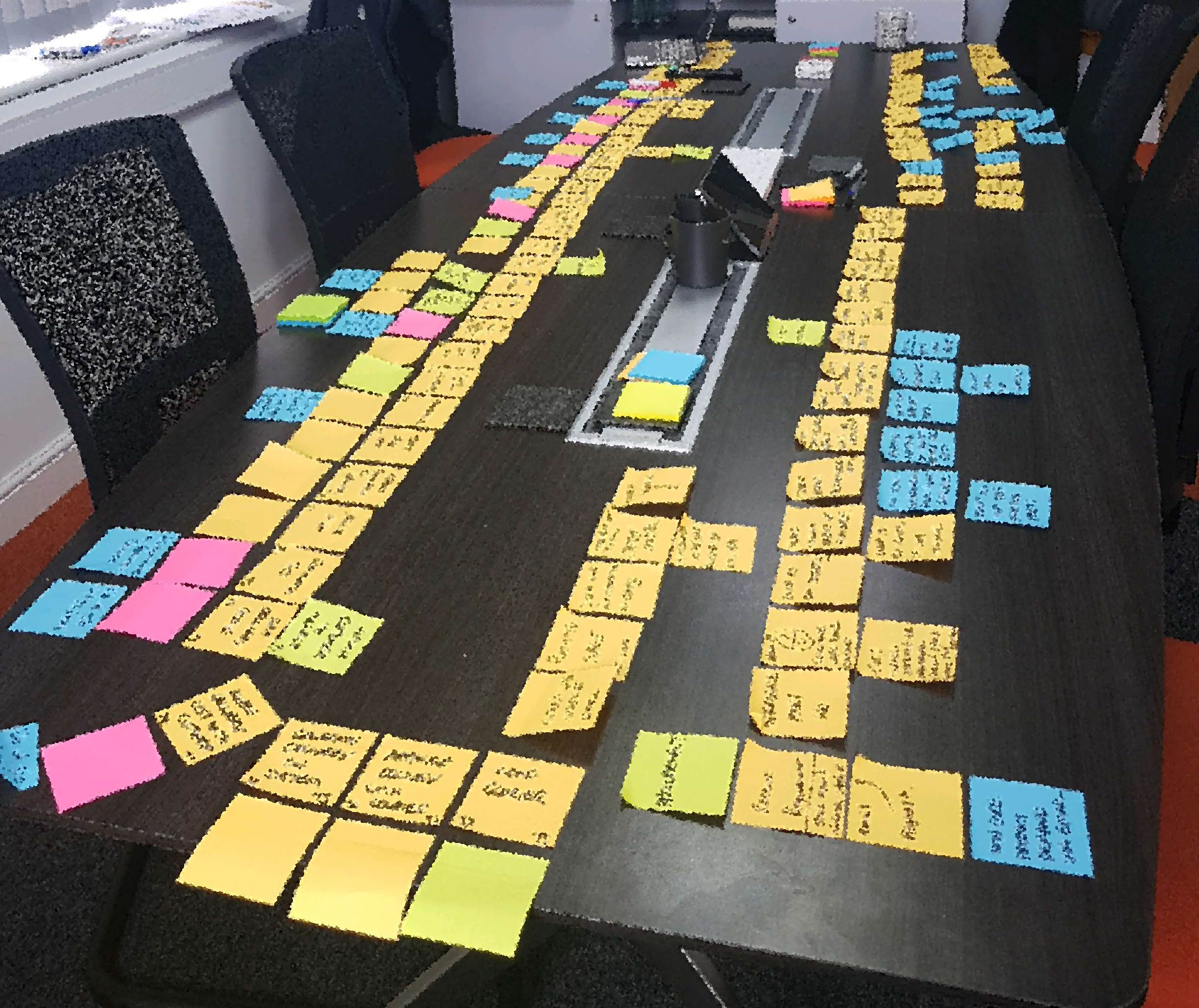
Business Discovery
A typical assignment will start with a Discovery workshop, and involves the development of the Enterprise Process Map - which is a simple summary of what goes on across the whole organisation, presented on one page. For each area, the top level process is then captured.
As the processes are being described, we capture opportunities for improvement. This may come from the team's experience, or be found by looking at the current activity through a lean lens. At high level, this asks:
- How does this process deliver what is the customer actually paying for?
- Does each step add value to the end product, and if not, can we minimise / get rid of it?
- How can we create a flow from the initial customer order (or request) through to final product?
- How can we minimise any work that isn't directly linked to a customer?
- What changes can we put in place so we are constantly improving the way we work?
The identified opportunities are then prioritised, and we discuss a plan that will enable the required changes to be made without disrupting business as usual activity.
Process Audits
For some businesses, there is simply a requirement to audit the existing processes and get some objective feedback on opportunities for improvement. In this situation, we carry out an engagement based on our Process Improvement Framework.
We assess each area on the framework from a standard set of questions which is a superset of ISO-9001, and has been developed to provide a process improvement perspective to the business.
The process audit report provides a RAG (Red, Amber, Green) rating for each area, along with supporting evidence and feedback.
Process Improvement Framework
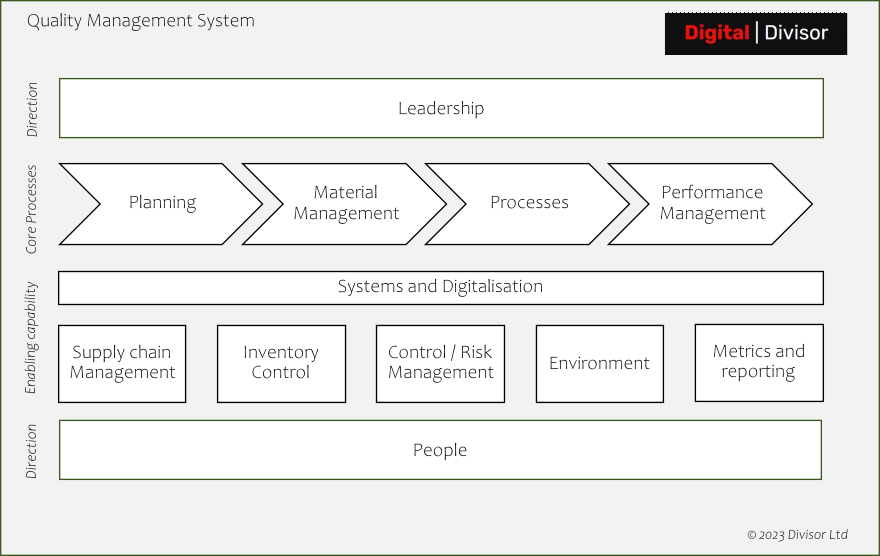
Improvement Delivery
We support the implementation of the process improvement plan through the delivery of 'kaizen' (change) workshops, which are focused on implementing the improvements. At the same time, we providing ongoing coaching - that keeps focus on what needs to be done, and provides a way for any challenges to be unblocked.
Value Stream Mapping
Value stream mapping may be used in business discovery or in improvement delivery and is a highly effective tool for analysing and improving processes - combining both a description of the core processes, and including process, lead time, headcount, inventory and other measures. Where there are specific products that are the focus of optimisation, we will use value stream maps as the basis for developing the improvement plan.
Deliverables
As outputs from a Process Optimisation engagement, you will typically receive:
Benefits
We have a goal to create a >5x return on investment for our clients. Additional benefits include:
Improved financial performance
The process optimisation review will result in a reduction / removal of activity that doesn't directly add value to clients or the business, resulting in greater efficiencies and lower unit labour costs. Value stream and other analysis of inventory and demand planning will reduce inventory levels, improving working capital.
Increased Efficiency
Your team will be more efficient, spending less time in meetings, focusing on priorities, and spending less time on tasks that can be simplified, automated or supported by digital tools. Optimising the design of key processes will then lead to improvements in your customer response times, product development times and process lead times.
Improved Employee Satisfaction
Process Optimisation engagements provide an opportunity for employees to identify, discuss and fix challenges in their roles, and by delivering engagements with the team, changes that are made are more likely to stick. Additionally, the development of Lean thinking increases the skills of the team, and creates opportunities for fulfillment, as they lead improvement activities.
Considerations
Timescales
The typical engagement will engagement will require approximately 7 days effort, which includes:
- A 1/2 day project briefing ('kick off') session
- A 2 day Discovery workshop
- A 1/2 day Optimisation Review and Planning workshop
- Preparation and write up of workshops
- Capture of the Enterprise Process Map
- Development of the Optimisation plan
Improvement delivery support will be tailored to client requirements, and is typically delivered in one or more 5-to-10 day phase(s).
Sustainability
Business optimisation covers the requirement to improve sustainability and reduce Scope 1, 2 and 3 emissions. During the Discovery phase, we look to identify opportunities to impact on the direct and indirect emissions created by a company and will include these in the Optimisation plan.
Interested in how we can help?
Get in contact